I Made Hand-Crafted Oxford Shoes. Was it Worth It?
- Katherine Sewing
- Jan 13, 2023
- 9 min read
Have you ever attempted something which made absolutely no logical sense, took about 100 years to complete, and felt ridiculously difficult? Well, that was the story of me hand-crafting a pair of Oxford shoes for my husband using traditional, historical shoe making techniques, natural materials, and a long labour of love!

I am obsessed with traditional hand shoe crafting, and making a pair of hand welted men's dress shoes has been on my list for a while. The first time I made a pair of hand welted shoes was actually my first pair of hand made shoes ever, and lets just say it did not go too well! Especially the hand welting part.
How did it turn out for this pair of shoes? Keep reading to find out! I will be sharing:
*How I adjusted a pair of shoe lasts to fit my husband's feet
*How I created the pattern for these shoes
*How I stitched the uppers on my new post bed sewing machine
*Lasting the shoes
*Attempting to hand welt a pair of shoes for only the second time ever
*Building the stacked leather heels, and finishing the shoes!
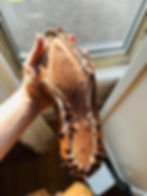
Stay tuned until the end to see if and how these shoes turned out, and to possibly get a peek at my husband wearing them! Let's jump into it.
Lasts and Pattern
The last comes first! I started with a pair of shoe lasts that I actually had bought for myself at least a year ago, from the lovely Vicky D'Incecco. There were in a classic men's wear shape, but ended up being too large for my feet. My husband's feet are not too much larger than mine, and so with a little building up with leather I was able to make these shoe
lasts fit the measurements of his feet. This involved gluing skived strips and patches of leather to the joint area of the lasts, as well as the toe area.
Once this was done, I created a standard pattern for these lasts by wrapping the last in masking tape, then carefully cutting off each half of this mould separately. After creating an average of these two halves, I was able to create a detailed oxford shoe pattern. I used a shoemaking textbook for these instructions. I cut out each component of this pattern individually out of cardstock, adding seam and folding allowance and marking the construction lines with small cut outs.
Now for the scary part: stitching together the shoe uppers!
Making the Shoe Uppers

Now it was time to cut out my leather pieces for the uppers! I used the same brown leather that I had used for my Downton Abbey shoes, and the same lining leather as well. I used saddle skirting for the soles, insoles, and stacked leather heels, and oak tanned belly leather for the shoe stiffeners.
After cutting, I skived the edges, and folded under edges where necessary. This gives a more polished appearance to any edges of leather that will be visible on the outside of the shoes. I used double sided shoemaking tape or glue to hold these edges in their new folded positions.
Then, it was time to stitch these shoe uppers together! This is called "closing the uppers". First I taped or glued the pieces of the shoe to be stitched together, then stitched them at my post-bed sewing machine. You don't need a post bed sewing machine for shoe-making, but I am thankful to have one! This was nerve-wracking and I went very slowly! I used my shoe-making textbook for its detailed directions on "closing" oxford shoe uppers.
Now for beginning the hand-welting process!
Carving the Welt and Lasting
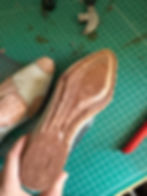
Now it was time to create our shoe insole! This is a more complicated process than creating an insole for cemented shoe construction, as it involves carving a "holdfast" into to hold the stitches, and the insole has to be thicker as well. The welt, or holdfast, is basically a ridge and a channel for the stitches to be held firmly in when we stitch the shoes together. This is also called the "feather". I used a knive, a gouger, and a feather knife to carry this out, and it was much smoother of a process than the first time I tried it! I then carefully marked and poked all of my stitching holes through the holdfast.
Next step: lasting the shoes. Lasting is the process whereby we take our at this point rather funny looking shoe uppers and draw them down tightly over the last, nailing and then gluing them in place. I explain this process thoroughly here. This forms the uppers around the 3D shape of the lasts, giving the shoes their final shape. Stiffeners are also inserted at the toe and heel areas to give extra support and structure.
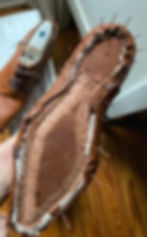
This was the trickiest part of this process, because the leather I used was not cooperating! You can read more about this on my Downton Abbey Shoes article. Needless to say, it was a process, with many imperfections along the way. It was at this point that I really had to step away from the goal of perfection, and simply try my best. After the lasting was done as best as I could, I glued down the uppers - ready for the next step: stitching the shoes together.
How I Learned Shoemaking
I am an entirely "self-taught" shoemaker, with most of what I currently know coming from great shoe-making and shoe history books. Here are several that I have found very helpful, with Amazon links to purchase:
Inseaming the Shoe
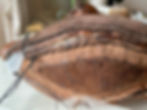
Now it was time to stitch together these shoes! This went much more smoothly than my first time trying it, partly due to experience and partly due to having better tools to work with. I used thick fishing line instead of needles, which I had to learn a unique process for attaching it securely and smoothly to the threads. I used what is known as "natural tapers" for my thread, bought from Lisa Sorrell, and black shoemaking wax. I also used a leather welt strip, which is the unifying piece that holds together the uppers, insole, and later the outsoles.

I would first poke my awl through the given stitch hole that I was working on, then chase it with one of my fishing line "needles" and threads. Then, I followed it with the second needle, so that the threads always criss crossed each other in each hole. This created a very attractive final product, with two lines of secure stitching visible on the bottom of the shoe. Needless to say, it took a long time.
Next - how on earth would I attach the outsoles and create stacked leather heels?
Attaching the Outsoles
It was time to attach our outsoles. First, I filled in the hollow area at the bottom of the shoe with a thin sheet of cork, glued in place. Then, I cut my outsoles out of thick, dense leather, and proceeded to thin down the edges with a knife and rough up the inside so it would adhere properly. I glued it in place, and then it was time to trim the sole and welt to fit the shoe.
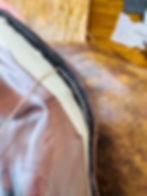
The welt strip was wider in some areas than I wanted it to be, and the sole was wider than the welt strip. Once these were trimmed down accurately, it was time for the second round of stitching! This time, the stitches would simply be through the welt strip and the outside of the sole, going straight up and down all around the shoe (excepting the heel area-more on that later). So, I marked the stitch holes carefully with a set of dividers, then poked each hole with my curved awl blade. I then stitched these holes using the same technique as earlier - one long thread with a fishing line "needle" on either end, with each thread end criss-crossing the other in each stitch hole. I used light coloured thread, but quickly realized that given my black coloured welt strip, black stitches would look better! So, after finishing the stitching, I carefully dyed the stitches black with leather dye and a paint brush.
Stacked Leather Heels and Final Touches
Let's talk about the heels. First, we have to rewind to an important step before attaching the outsoles. Creating the rand. What is a rand? It is a horseshoe shaped piece of leather, skived down to nothing at the inside edge, curved around the heel area of the shoe, and glued and pegged in place. This levels out the heel area, which would otherwise be somewhat convex. After attaching the outsole, I began the heel with a second rand, to complete the levelling out process and to create a firm foundation for the heels. What were the heels made of? Leather! Many pieces of stacked up sole leather, glued and pegged in place.
I started with several heel "lifts" cut out and prepped by roughing up each side so it would glue properly. I then glued one lift in place, trimmed it carefully with a knife, and pegged it in place, before moving on to the next lift. This was a much easier process than in my 1820's boot making, where I glued them all together before beginning the shaping process. For the final heel piece, I used a thicker leather, and added a partial rubber heel piece to the back outside of the heel piece that typically sees the most wear. Later, this entire bottom heel piece was nailed in place.
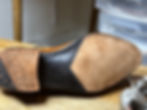
The thing about shoe-making is that even when you reach a point where you feel you should be finished, there is still much work to do, and arguably the most important parts - “finishing” the shoe. This involves rasping, sanding, and burnishing everything mirror-smooth, before applying any finishing dyes or polishes. After I got the edges of the sole and heel as smooth as possible through first rasping, then sanding with progressively finer grits of paper, and finally burnishing and hammering the leather fibres flat, it was time to dye. I chose to dye the sides of the heels, the edges of the sole, and the waist area of the sole black, before applying black burnishing wax and polishing everything to a very shiny finish.

The last step was removing the shoe lasts which I had a lot of trouble with and in fact almost despaired about getting the lasts out with the shoes intact. I need to figure something out so that it is easier next time! Then, I applied a “sock liner”, which is a piece of lining leather cut to fit the shape of the insole, and glued inside the bottom of the shoes. This gives a more polished appearance to the finished shoes. Time to try on the finished shoes!
All Finished!
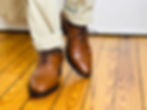
My husband has been wearing these shoes every week, and though they are a little snug (my bad), we both love how they turned out. What would I do differently next time? Well, the main thing is that I’ve learned I don’t like working with this particular type of leather - it doesn’t respond well at all to being wet and so the uppers are not as flawless as I would have liked. That being said, I still have a lot more of this leather and have learned some methods of working with it to (hopefully) minimize issues next time.
I would probably use dedicated mens dress shoe lasts next time, and make extra sure that they fit the feet properly, possibly by creating an actual test shoe first. I would also use smaller nails on the finished heels next time.

What did I learn? I love stitching shoes together! Even though it takes so long and it has a very narrow margin of error, it is so meditative and calming of a process. I honestly felt like I was tapping into some part of my ancestry through stitching these shoes together. Who knows, I could have very easily had an ancestor who was a shoe maker!
I will also say that learning shoe-making, although very different from sewing, has actually improved my sewing skills. That is because shoemaking has helped me become better at accuracy and extreme attention to detail, which has never been my strong suit, and therefore helped me be a better and more accurate seamstress as well.
Conclusion
I hope you found this article entertaining and helpful! Pictured above is the very first pair of shoes I made in early 2021, compared to now, my 6th finished pair. I've come a long way!
Be sure to sign up for my email newsletter if you haven’t already, especially if you appreciate vintage and historical sewing, shoemaking, and natural hair care.

If you would like to help in a small way to support this channel and me as a busy mom to continue producing content, feel free to “buy me a coffee” using one of the buttons in this article. Thanks, I really appreciate it!
Finally, I have an exciting announcement, related to my Youtube channel! I have just recently set up a Youtube membership. If you hadn’t heard, Youtube membership is a way to personally support your favourite content creators, in exchange for exclusive content. You can join my channel here.
So, for my membership program, you will receive:
For the first tier of support: 24 hours of early, ad-free access to my newest video releases, as well as an exclusive chat group, and at least two exclusive insider posts per month.
For the second tier of support, you will additionally have access to a monthly exclusive livestream with me where I will personally answer any of your questions about sewing, hair care, or anything in between. Most excitingly, you will have a sway on future video topics! Please consider joining as if enough of you do, it would significantly help support me, this channel, and my family, so I can continue producing content for you as a busy mama. You can join my channel here.
Click here for the full list of sewing products I recommend. Click here for the full list of hair-care products I recommend. I have personally used all of these products and can wholeheartedly recommend them to you. It also helps support this blog if you purchase anything through one of those links because I receive a small commission at no extra cost to you.
Contact me at katherine@katherinesewing.com